GMP Equipment FAT’s – Let’s Talk About It
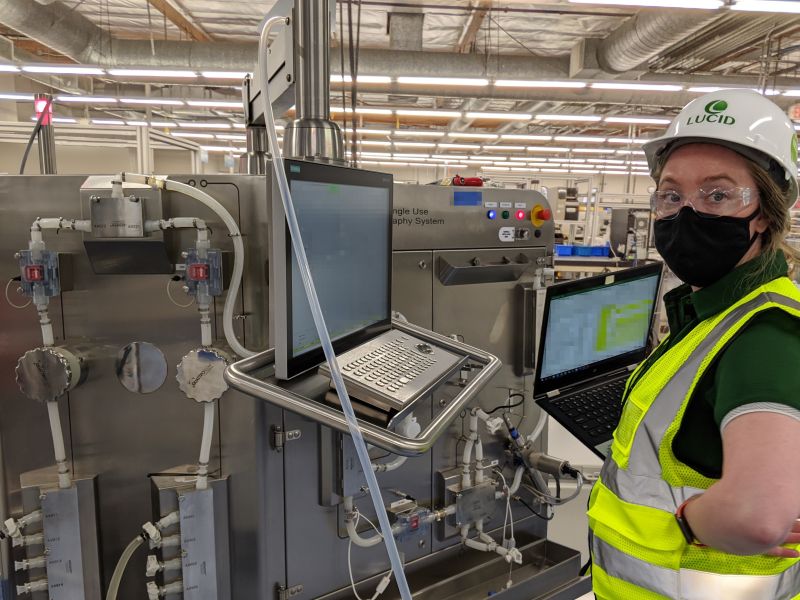
GMP Equipment FATs, big issue… let’s talk about it. OEM’s have great sales teams, but we’ve been seeing the operations teams struggling. Factory Acceptance Testing is the first gating event to ensure you receive what you think you ordered.
First off, don’t skip the FAT! IIt costs magnitudes less to fix issues in the OEM’s shop. Yes, traveling can be inconvenient, but it’s far better than working long hours to meet a shrinking shutdown window to bring this equipment online.
Secondly, insist on being a reviewer/approver on the design documents and acceptance testing, even if the OEM has a standard package.
This is your early opportunity to evaluate the quality systems in place. Are the documents detailed enough for design, or are they glorified user manuals?
Are the test forms actually testing your process requirements, or are they just testing their proprietary equipment configuration?
When you arrive, bring a kit to verify that the external interfaces will function within your facility’s infrastructure.
Can Ethernet IPs be changed? Are OPC UA certificates configured? Are ports for VNC/RDP open? Trust me, these are terrible finds once the equipment is in place.
Your responsibility is to ensure that the equipment leaving the factory is ready for integration. This approach saves time, money, rework, and, most importantly, protects your schedule.
I recommend having a trusted integration partner assist with this. Our clients have significantly reduced startup costs by involving us from the RFP stage.
Startups are hard enough. A good FAT goes a long way in making it easier for everyone.