How to Factory Test With Your Site Infrastructure
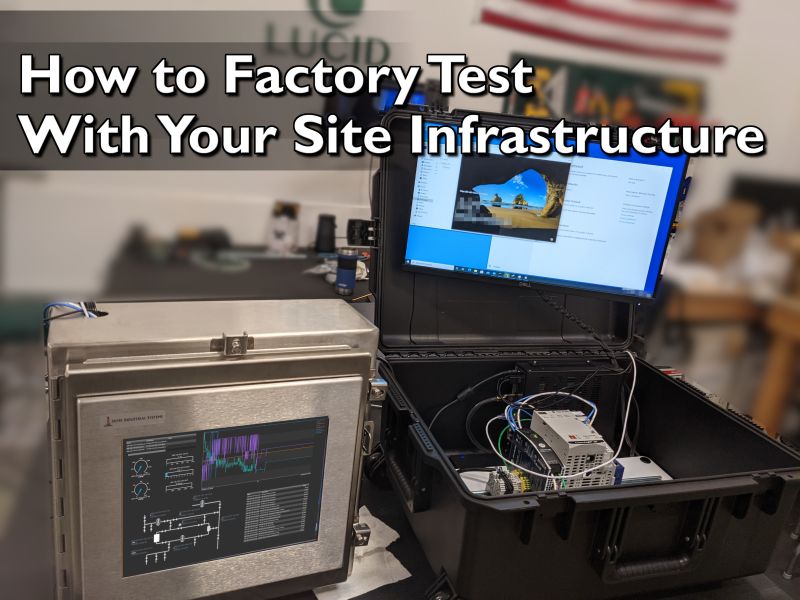
No equipment exists on an island. Sooner or later, process data and audit logs must connect to your facility’s infrastructure. Fixing integration issues during FAT is far cheaper than troubleshooting after the equipment arrives on site.
To streamline that process, we developed the PRO Mobile Station: a rugged unit with a CompactLogix PLC, managed switch, and a PC workstation capable of running up to six virtual machines.
We load whatever platforms our clients use—Rockwell FT View SE, ThinManager, Historian, Active Directory, SQL, Wonderware, Ignition, PI Vision, Dream Reports, and other site‑specific tools—essentially bringing the plant infrastructure to the vendor’s floor. This lets us spot issues early, including:
1. OPC UA setup
2. Licensing issues (Installed vs. what was ordered)
3. Thin client resolution issues / Thin Manager compatibility
4. Alarm floods or audit trail verbosity
5. Tagging and paths for historian tags
6. Characterization of data bandwidth or VLAN configurations
7. Domain Security groups
We include a PRO station as an option during bidding. Turns out it makes a great development station and training platform after the equipment is on site.
Making your own is pretty straight forward. But we realize time is money and ours comes ready‑to‑roll complete with rugged hardware and our setup expertise.
Whichever way you go, be proactive. Bring your infrastructure to the FAT.
Your future self will thank you for the saved budget, schedule, and headaches.
https://www.linkedin.com/feed/update/urn:li:activity:7325553733684056065